INCOMPLETE PENETRATION
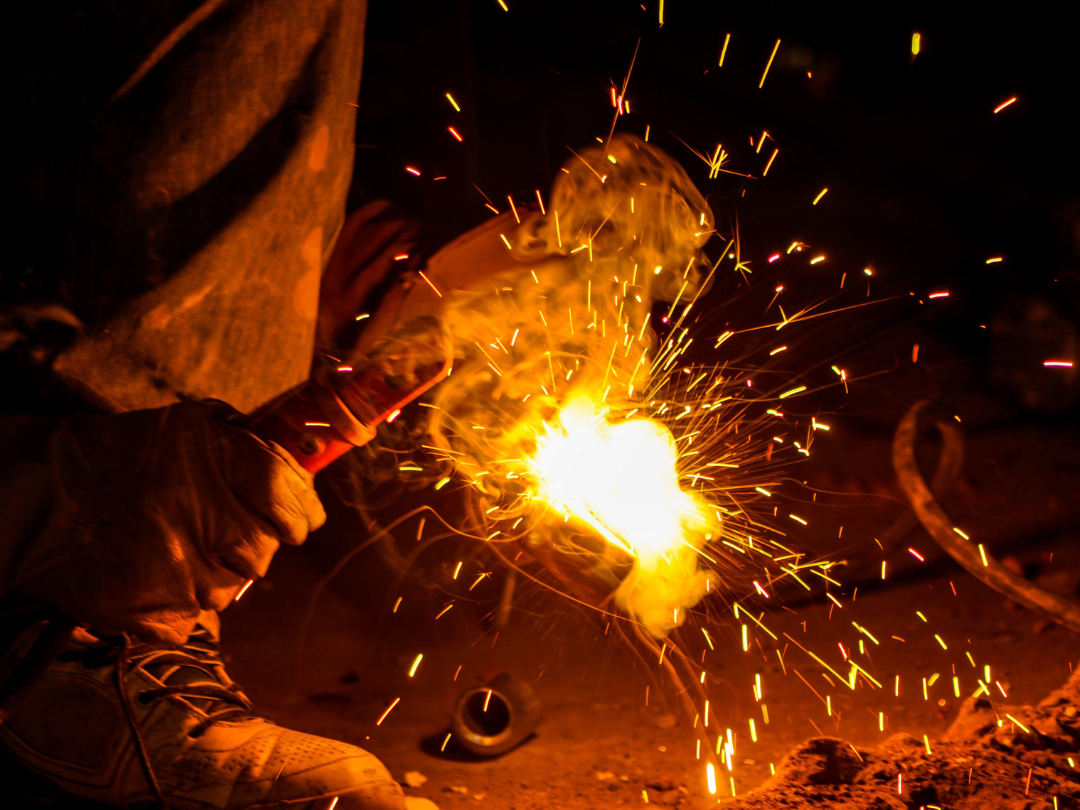
Welding is a complex and crucial process in various industries, ensuring the integrity and reliability of joints in structures and components. However, like any manufacturing technique, welding is susceptible to defects, one of which is incomplete penetration. In this article, we delve into the nuances of incomplete penetration, exploring its causes, preventive measures, and the solutions that Steel City NDT can provide to maintain the highest welding quality standards.
Incomplete penetration in welding occurs when the weld metal fails to extend through the entire thickness of the joint. In simpler terms, it means that the weld does not fully penetrate or bond with the base material. This welding defect can manifest in various forms and is often a result of several contributing factors.
Causes of Incomplete Penetration
- Incorrect Welding Parameters: One of the primary culprits behind incomplete penetration is the use of incorrect welding parameters. Welding parameters encompass variables such as voltage, current, and travel speed. When these parameters are not set correctly for the material and thickness being welded, the weld may not penetrate fully.
- Poor Joint Design: The design of the joint itself plays a crucial role in achieving complete penetration. A poorly designed joint, with inadequate access for the welding process, can hinder the weld metal from reaching the required depth.
- Incorrect Filler Material: The choice of filler material is another contributing factor. It must be compatible with the base material and have the appropriate melting temperature to ensure complete fusion and penetration.
Preventing Incomplete Penetration
Preventing incomplete penetration is essential for maintaining the structural integrity of welded components. Here are some key preventive measures:
- Correct Welding Parameters: Ensure that the welding parameters are meticulously set according to the material and thickness being welded. This includes adjusting voltage, current, and travel speed to achieve the desired penetration.
- Appropriate Filler Material: Select a filler material that is not only compatible with the base material but also has a melting temperature that aligns with the welding process. This ensures that the filler material effectively fuses and penetrates the joint.
- Optimal Joint Design: Pay close attention to joint design, ensuring that it facilitates complete penetration. Proper access for the welding process is crucial, as it allows the weld metal to reach the required depth.
Consequences of Incomplete Penetration
Incomplete penetration is a welding defect that should not be taken lightly. If left unaddressed, it can compromise the strength and integrity of the weld, leading to structural failures or performance issues in the welded component. To prevent such consequences, it is imperative to prioritize the correct welding parameters, suitable filler materials, and sound joint design.
In conclusion, incomplete penetration is a welding defect that warrants meticulous attention to detail and preventive measures. Steel City NDT understands the critical importance of welding quality and offers a range of non-destructive testing services to detect and rectify defects like incomplete penetration. By adhering to best practices and ensuring proper welding techniques, we ensure that your welded components meet the highest standards of safety and reliability, contributing to the success of your industrial operations.