The Most Effective Forms of Non-Destructive Testing
July 5, 2024
In the world of manufacturing and construction, quality control is paramount. One key aspect of this is the testing of materials and components.
Non-destructive testing (NDT) plays a crucial role in this process. It allows for the inspection of materials without causing damage or altering their functionality.
In this article we'll dive into the most effective forms of NDT. We'll explore methods such as visual inspection, eddy current testing, and more.
Each method has its unique advantages and applications. Understanding these can help professionals choose the right approach for their specific needs.
Whether you're a seasoned engineer or a student in the field, this guide will provide valuable insights. Let's dive into the fascinating world of non-destructive testing.
Understanding Non-Destructive Testing (NDT)
Non-Destructive Testing (NDT) is a broad group of analysis techniques. These techniques are used in science and industry to evaluate properties of a material, component, or system.
The key aspect of
NDT is that it does not cause any damage to the material being inspected. This is in contrast to destructive testing methods, which can alter or even destroy the material.
NDT methods include:
- Visual inspection
- Eddy current testing
- Magnetic particle testing
- Liquid penetrant testing
- Radiographic testing
- Ultrasonic testing
Each of these methods has its unique applications and benefits. They are used across a wide range of industries, from aerospace to construction.
The Importance of NDT in Industry
NDT is vital in ensuring the safety and reliability of materials and components. It helps detect defects that could lead to failure, preventing accidents and costly repairs.
In industries such as
aerospace or
automotive, NDT is crucial. It ensures the integrity of critical components, contributing to the safety of vehicles and aircraft.
Moreover, NDT plays a significant role in quality control. It helps maintain high standards of production, ensuring that products meet the required specifications.
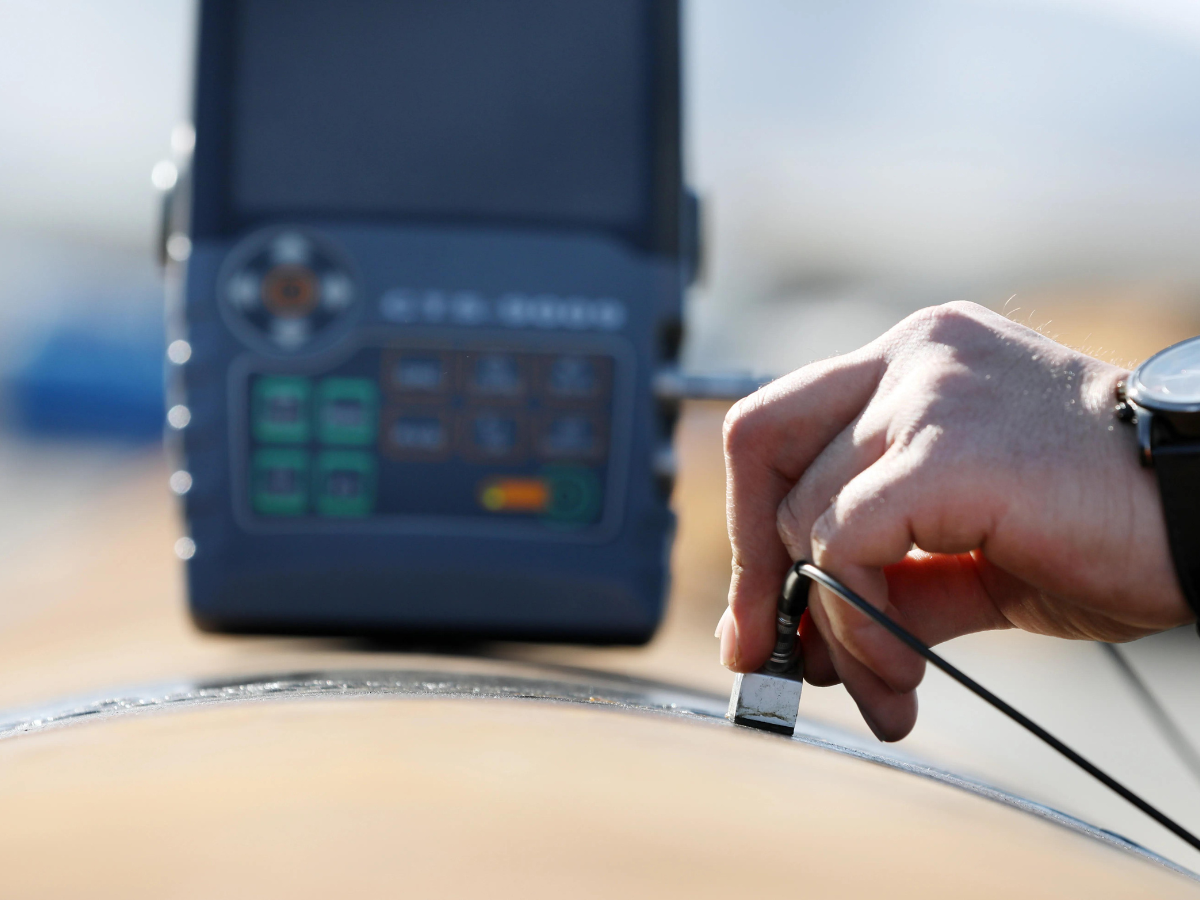
Photo By: Universal Technical Institute
Key Principles of NDT Methods
NDT methods are based on the interaction of energy with a material. They can detect, measure, or evaluate flaws, properties, or conditions without causing damage.
The choice of an NDT method depends on the type of defect and the material. For instance, magnetic particle testing is used for
ferromagnetic materials, while ultrasonic testing is suitable for a variety of materials.
Understanding the principles of each method is crucial. It helps professionals choose the right approach for their specific needs, ensuring effective and accurate testing.
Visual Inspection: The First Line of Defense
Visual inspection is the simplest and most common form of NDT. It involves examining a component or structure directly with the naked eye or using optical aids.
This method is often the first step in the inspection process. It can identify obvious defects such as cracks, corrosion, or misalignments.
Despite its simplicity, visual inspection requires trained personnel. They need to understand what to look for and how to interpret what they see.
Eddy Current Testing: Detecting Surface Flaws
Eddy current testing is a non-contact method used to detect surface and near-surface defects. It uses electromagnetic fields to induce eddy currents in the material under inspection.
These currents create a magnetic field that interacts with the original field. Any changes in this interaction can indicate a defect.
This method is particularly useful for inspecting
conductive materials. It's often used in industries such as aerospace and automotive for detecting cracks or corrosion.
Magnetic Particle Testing: Exploring Ferromagnetic Materials
Magnetic particle testing is a method used to detect surface and near-surface defects in ferromagnetic materials. It involves magnetizing the material and applying magnetic particles to the surface.
The particles are attracted to areas where the magnetic field is distorted, indicating a defect. This makes it easy to visualize and locate any flaws.
This method is widely used in industries such as construction and manufacturing, where it's crucial to ensure the integrity of structures and components.
Liquid Penetrant Testing: Unveiling Hidden Cracks
Liquid penetrant testing is a non-destructive testing method used to detect cracks and other surface discontinuities in non-porous materials. It involves applying a liquid with high surface wetting characteristics to the surface of the test object.
The liquid penetrates into any surface-breaking defects and is then drawn back to the surface by capillary action when a developer is applied. This makes the defects visible to the naked eye.
This method is particularly useful for materials that are not suitable for other types of NDT, such as
non-magnetic materials or plastics.
Radiographic Testing: Seeing Beneath the Surface
Radiographic testing is a non-destructive testing method that uses X-rays or gamma rays to inspect the internal structure of a material. It works by exposing a test object to radiation and capturing the resulting image on a detector.
The image reveals variations in material thickness, changes in density, and the presence of internal defects. This method is highly effective for detecting internal flaws that are not visible on the surface.
It's widely used in industries such as aerospace, automotive, and oil and gas for quality control and safety checks.
Ultrasonic Testing: High-Frequency Insight
Ultrasonic testing is another non-destructive testing method that uses high-frequency sound waves to detect defects. It works by sending sound waves into a material and measuring the time it takes for the waves to return.
This method is particularly effective for detecting internal flaws and measuring the thickness of materials. It's commonly used in industries such as aerospace, automotive, and manufacturing for quality control and safety checks.
Material Inspection: Ensuring Safety and Reliability
Material inspection is a critical aspect of non-destructive testing. It ensures the safety and reliability of structures and components by detecting defects before they lead to failure.
This process is vital in industries such as construction, aerospace, and automotive, where the integrity of materials can directly impact safety and performance.
Comparing NDT Methods: Sensitivity, Accuracy, and Cost
When choosing an NDT method, several factors come into play. Sensitivity, accuracy, and cost are among the most important considerations.
Sensitivity refers to the method's ability to detect small defects. Some methods, like radiographic testing, are highly sensitive and can detect minute flaws. However, these methods may also be more costly and require specialized equipment and trained personnel.
On the other hand, methods like visual inspection are less sensitive but more cost-effective.
They can be performed with minimal equipment and training, making them suitable for routine checks and maintenance. The choice of method ultimately depends on the specific requirements of the task at hand.
Conclusion: Steel City NDT - Your Trusted Partner in NDT Services
As we conclude our exploration of the most effective forms of non-destructive testing, it is evident that ensuring the safety and reliability of materials and components is paramount in various industries. At Steel City NDT, we understand the critical role that non-destructive testing plays in quality control and defect detection.
With a commitment to excellence and innovation, Steel City NDT stands out as a trusted partner for all your non-destructive testing needs. Our team of experienced professionals utilizes cutting-edge technology and industry-leading NDT methods to provide accurate and reliable inspection services.
By choosing Steel City NDT, you can rest assured that your materials and structures are in capable hands. Our dedication to safety, quality, and customer satisfaction sets us apart as a leader in the NDT industry.
Contact Steel City NDT today to experience the difference in precision, efficiency, and reliability in non-destructive testing services. Partner with us for a safer and more reliable future in manufacturing and construction.
You might also like
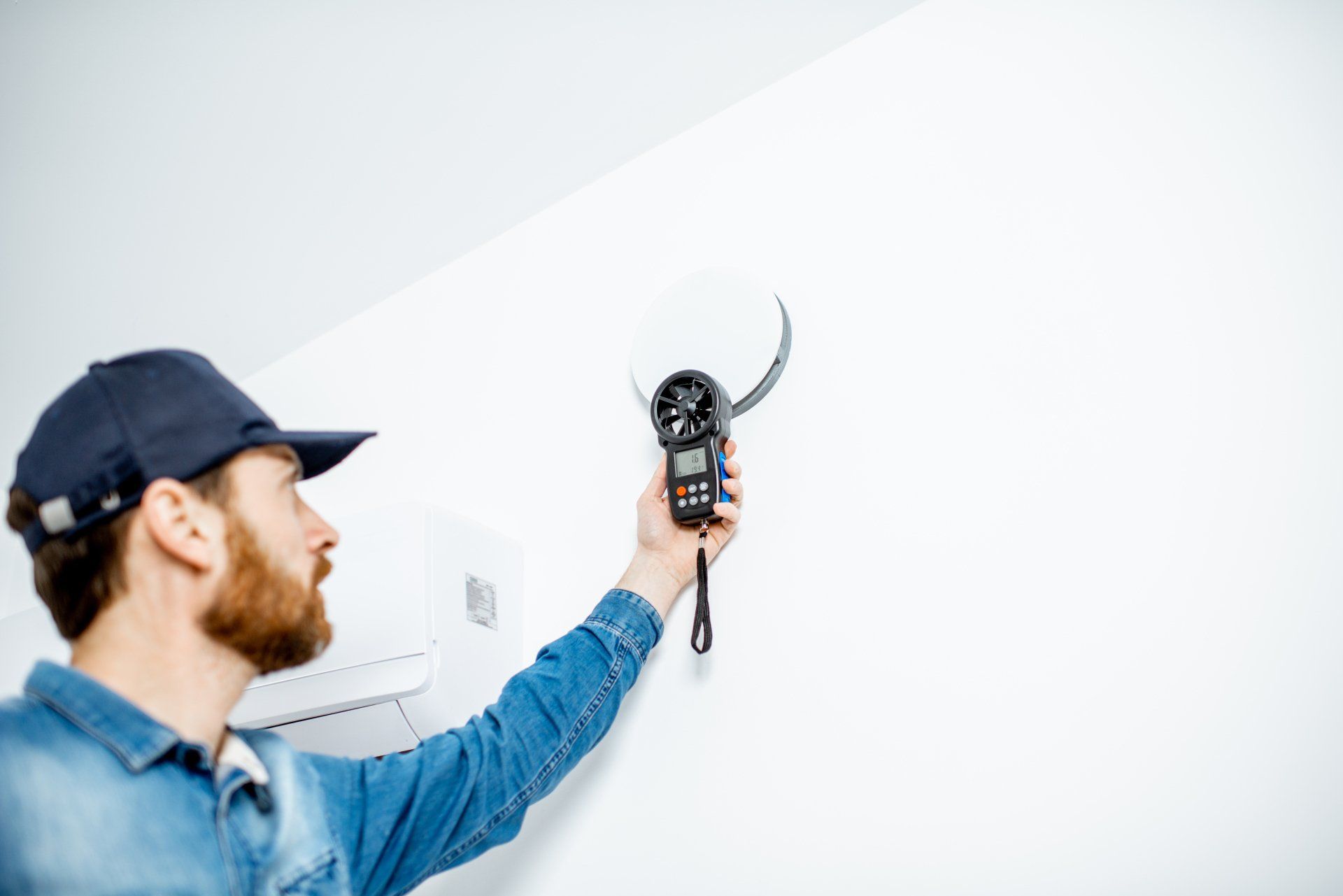