UNDERCUT
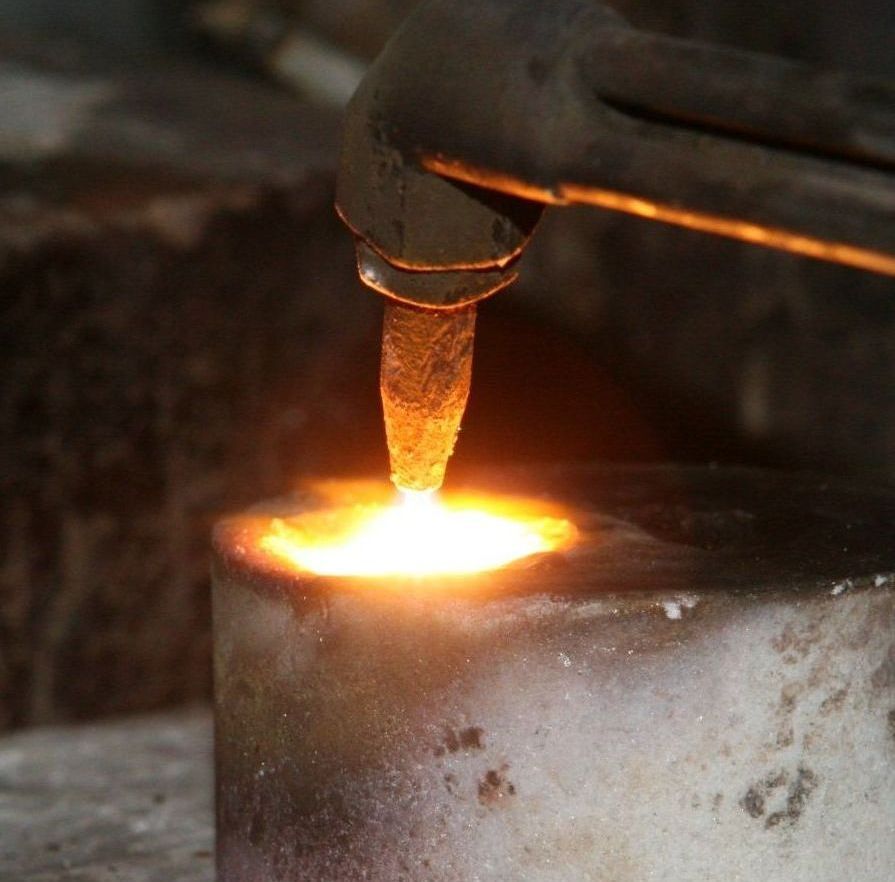
In the realm of certified welding inspection, the term "undercut" holds significant weight, representing a potential threat to the integrity of a welded joint. Undercut refers to the groove or depression formed along the edge of the weld bead, where the base metal has melted but hasn't been adequately filled by the filler metal. This seemingly minor defect can have profound consequences, leading to a weakened joint susceptible to cracking, corrosion, and failure, especially under cyclic loading conditions. The presence of undercut in a welded joint is a cause for concern as it results in a groove that diminishes the cross-sectional thickness of the base metal. This reduction in thickness translates to a weakened workpiece, compromising the structural integrity of the entire assembly. The consequences of undercut are particularly severe in critical applications where the weld is subjected to stress and strain.
Several factors contribute to the formation of undercut, making it imperative to identify and address the root causes during certified welding inspections. Common culprits include excessive welding current, the use of incorrect filler metal, and poor welding technique. Excessive welding current can lead to excessive melting of the base metal, creating an undercut. Using filler metal that doesn't match the specifications outlined in the welding procedure can result in inadequate filling of the weld groove, leading to undercut. Inadequate welding technique, such as improper manipulation of the welding gun or erratic movement during the welding process, can contribute to the formation of undercut.
Visual weld inspection emerges as a critical process in identifying and mitigating undercut and other defects. This inspection method involves the observation of a weld with the naked eye or through devices with varying levels of magnification. Its significance lies in ensuring that the weld adheres to the requirements outlined in the welding procedure specification (WPS). Visual inspection is a fundamental aspect of quality assurance in welding, allowing inspectors to identify defects like undercut early in the process, preventing the propagation of issues throughout the entire weldment. By closely examining the weld, inspectors can verify if it meets the specifications outlined in the welding procedure, crucial for ensuring that the final product is fit for its intended purpose. Identifying and addressing undercut during visual inspection helps prevent costly failures down the line, as catching defects early allows for necessary corrective measures before the welded component is put into service. In conclusion, understanding and addressing undercut in certified welding inspections are vital for ensuring the structural integrity and longevity of welded joints. Through thorough visual weld inspections, potential defects can be identified early, allowing for corrective actions that contribute to the overall success and reliability of the welding process.